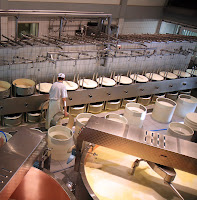.jpg)
One
of the only ways to sustainably improving quality or reducing waste is to have a
culture of efficiency built into your organisation. But how do we best to create this?
Ideally this business culture needs to be built from the roots up, as its the employees with the power to create real
sustainable change within the organisation. They need to be
self-motivated and care about the quality of the products being produced, as
they are the driving force behind driving the standards in your organisation. If they believe in the culture of the business then your
more likely to get successes. However if this is not supported by a top down
approach it is bound to failure.
The other important aspect is
having quality control and assurance processes in place to aim towards zero
defect production and increased efficiency. As well as kaizen, 6 sigma,
continuous improvement initiatives, quality circles and benchmarking companies
should not rest on their laurels, they should always be looking for ways to
improve.
Quality operations management for the plant floor is one way of doing
this. This increases operational efficiency with improved accuracy of quality
data and reduced cost of quality, offers higher operational agility while
securing compliance and safety as well as reducing losses through tighter
control and faster response times to deviations.
For more information download our
Quality Operations Management for the Plant Floor Webinar
Helena Finnan, Marketing Manager - Software, SolutionsPT
Amy, very interesting article! Would love to have you as a guest blogger at blog.wonderware.com. Perhaps a case study/brief coverage of a customer success story.
ReplyDelete